Why Mechanical Testing After Heat-Treatment is Essential for Steel and Aluminum Parts
Steel and aluminum are two metals ubiquitously used in various industries, from automotive to aerospace and construction to consumer electronics. One of the critical processes these metals undergo before final use is heat-treatment. This process alters the metallurgical structure of the material, aiming to enhance specific properties like strength, hardness, or ductility. However, it’s vital to ensure that these properties are achieved accurately. This is where mechanical testing, such as tensile testing or Charpy testing, comes into play.
Verification of Material Properties:
- Tensile Testing: By applying a controlled force until failure, tensile testing helps in determining the ultimate tensile strength, yield strength, and elongation of the metal. This ensures that after heat-treatment, the material meets or exceeds the expected strength and ductility levels.
- Charpy Testing: This measures the amount of energy absorbed by a material during fracture. It’s crucial for assessing the toughness of the metal, which reflects its ability to resist shock or impact.
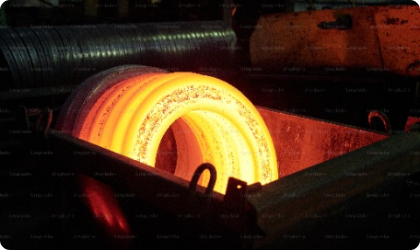
Evaluating Metallurgical Changes:
Heat-treatment induces phase transformations in metals. For instance, steel can transition between ferrite, austenite, martensite, etc. Mechanical tests can indirectly indicate whether the desired metallurgical phase was achieved, as each phase corresponds to distinct mechanical properties.
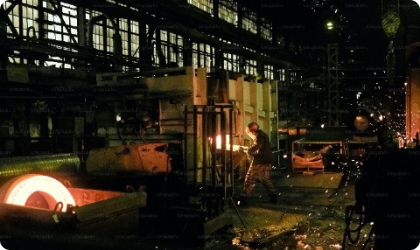
Ensuring Consistency & Uniformity:
Different sections of a component might react differently to heat-treatment, leading to non-uniform properties. Mechanical testing can identify these inconsistencies, ensuring that the entire component has the desired properties.
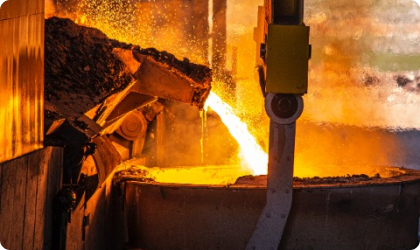
Avoiding Potential Failure in Service:
Undetected flaws or unmet mechanical properties can lead to catastrophic failures in real-world applications. Testing helps in early detection, ensuring safety and reliability.
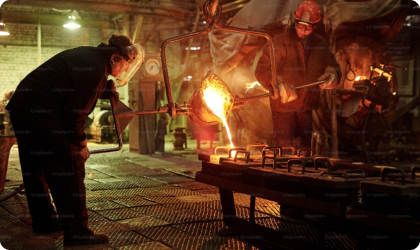
Feedback for Process Optimization:
If the desired properties aren’t achieved, mechanical tests provide feedback. This can be used to fine-tune the heat-treatment process, such as altering temperature or soaking time, to ensure optimal results in subsequent batches.
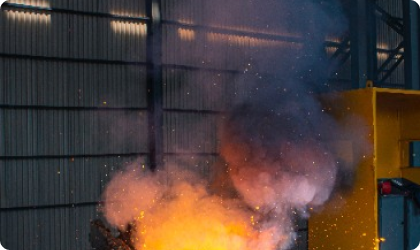
Compliance with Standards:
Industries often follow set standards (e.g., ASTM, ISO) which define the required mechanical properties for specific applications. Mechanical testing ensures that these standards are met post heat-treatment.
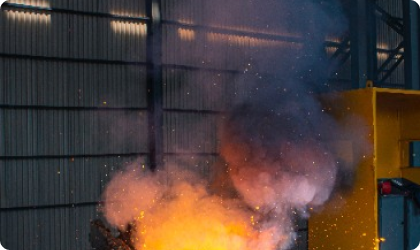
ThermTech through our in-house laboratory and relationships with outside laboratory services offers a full menu of testing and metallurgical consultation. Whether the goal is development, problem solving or quality control ThermTech is a one stop shop for metallurgical testing and analysis.
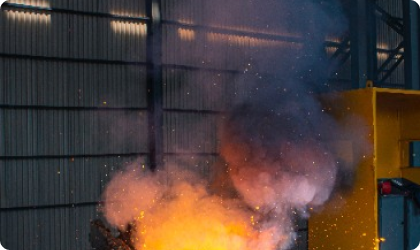
Capability
ThermTech’s lab is oriented towards testing hardness and microstructural analysis. Recent investments include a state of the art Leco micro-hardness tester that is completely automated eliminating any error due to measuring the hardness impression. Computerized image analysis tools for measuring grain size and microstructural elements are available as well. ThermTech is well versed in all forms of hardness testing.
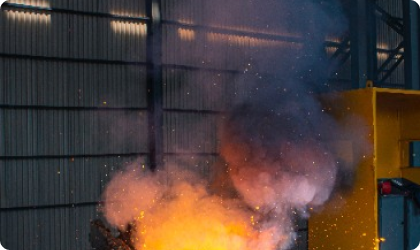
Process
One of the principal reasons for heat treatment is to change mechanical properties. Thus it is critical to have the tools available to evaluate the changes in microstructure and hardness that forecast final mechanical properties. It is extremely important that a competent team of professionals is on staff that will leverage these tools to provide for a properly heat treated component yielding the metallurgical design criteria. ThermTech has the tools and talent to provide our customers with the best products and advice!
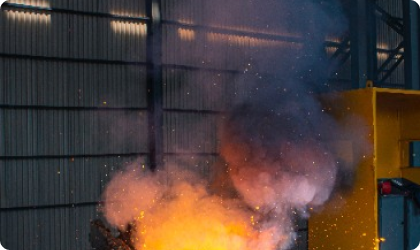
Recommendations
While ThermTech does not have in-house capabilities to test for mechanical properties we have mature relationships with a number of A2LA accredited laboratories. When product needs mechanical testing, post heat treatment, ThermTech can easily take care of all mechanical testing needs, providing the customer a heat treated part with certifications meeting all required properties.
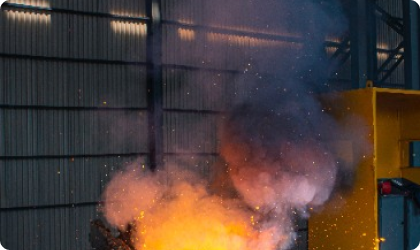
Conclusion:
Mechanical testing post heat-treatment isn’t just a procedural step; it’s a necessity. It ensures that steel and aluminum parts achieve the desired mechanical properties, ensuring their reliability, safety, and durability in real-world applications.
ThermTech outsources all mechanical testing to labs that have achieved ISO 17025 certification with a relevant scope and are compliant in processing ITAR parts and are A2LA approved.
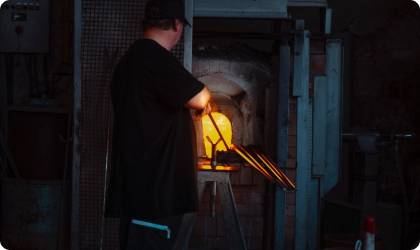